The reducer is to match the speed and transmit the torque between the prime mover and the working machine or the actuator. The reducer is a relatively precise machine. The purpose of using it is to reduce the speed and increase the torque. However, the working environment of the reducer is quite harsh. Faults such as wear and leakage often occur. Today, XINDA Motor will share with you a few tips for reducer maintenance!
1. Work Time
work , when the temperature rise of the oil exceeds 80°C or the temperature of the oil pool exceeds 100°C or abnormal noise is generated, stop using it. Check the cause and eliminate the fault. Replacing the lubricating oil can continue to operate.
Xinda Motor shares with you the maintenance skills of the reducer.
2. Change the oil
When changing the oil, wait until the reducer cools down and there is no danger of burning, but it should still be kept warm, because after cooling, the viscosity of the oil increases and it is difficult to drain the oil. Note: Cut off the power supply of the transmission to prevent unintentional power-on.
3. Operation
After 200~300 hours of operation, the oil should be changed. In the future use, the quality of the oil should be checked regularly, and the oil mixed with impurities or deteriorated must be replaced in time. Under normal circumstances, for a reducer that works continuously for a long time, the oil should be changed after 5000 hours of operation or once a year. For a reducer that has been shut down for a long time, the oil should also be replaced before re-running. The reducer should be filled with the same grade of oil as the original grade, and must not be mixed with oil of different grades. Oils of the same grade but with different viscosities are allowed to be mixed.
4. Oil spill
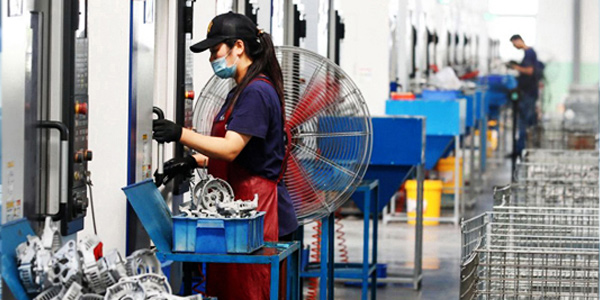
4.1. Pressure equalization
The oil leakage of the reducer is mainly caused by the increase of pressure in the box, so the reducer should be equipped with a corresponding ventilation cover to achieve pressure equalization. The ventilation hood should not be too small. The easiest way to check is to open the upper cover of the ventilation hood. After the reducer runs continuously at high speed for five minutes, touch the ventilation opening with your hand. When you feel a large pressure difference, it means that the ventilation hood is small and should be enlarged. Or raise the fume hood.
4.2. Smooth flow
Make the oil sprinkled on the inner wall of the box flow back to the oil pool as soon as possible, and do not keep it in the seal of the shaft head, so as to prevent the oil from gradually leaching out along the shaft head. For example, an oil seal ring is designed on the shaft head of the reducer, or a semi-circular groove is glued on the upper cover of the reducer at the shaft head, so that the oil splashed on the upper cover flows to the lower box along the two ends of the semi-circular groove.
(1) Improvement of the shaft seal of the reducer whose output shaft is a half shaft The output shaft of the reducer of most equipment such as
belt conveyors , screw unloaders, and impeller coal feeders is a half shaft, which is more convenient for modification. Disassemble the reducer, remove the coupling, take out the shaft seal end cover of the reducer, machine the groove on the outer side of the original end cover according to the size of the matching skeleton oil seal, and install the skeleton oil seal with the side with the spring facing inward. When reassembling, if the end cover is more than 35 mm away from the inner end face of the coupling, a spare oil seal can be installed on the shaft outside the end cover. Once the oil seal fails, the damaged oil seal can be taken out, and the spare oil seal can be pushed into the end cover. Time-consuming and labor-intensive processes such as dismantling the reducer and dismantling the coupling are omitted.
(2) Improvement of the shaft seal of the reducer whose output shaft is the whole shaft. The output shaft of the reducer with
the whole shaft transmission has no coupling. If it is modified according to the plan (1), the workload is too large and it is not realistic. In order to reduce the workload and simplify the installation procedure, a split-type end cover is designed, and an open-type oil seal is tried. The outer side of the split end cover is machined with grooves. When installing the oil seal, take out the spring first, saw off the oil seal to form an opening, put the oil seal on the shaft from the opening, connect the opening with adhesive, and install the opening upwards. Install the spring and push in the end cap.
5. How to use
User should have reasonable rules and regulations for use and maintenance, and should carefully record the operation of the reducer and the problems found in the inspection, and the above regulations should be strictly implemented. The above are the maintenance skills of the reducer.
Post time:
Feb-08-2023