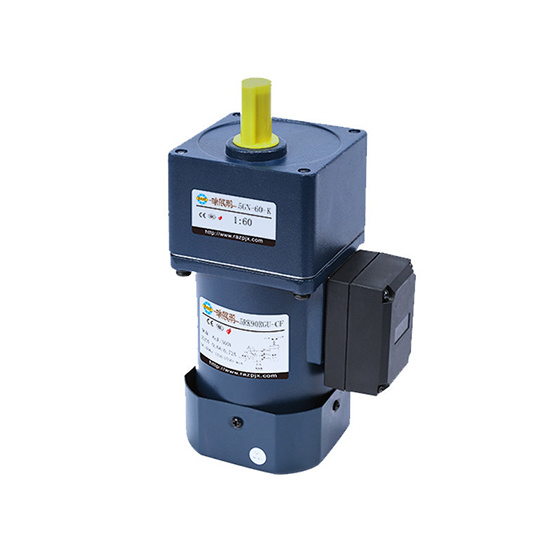
Micro reduction motor manufacturers talk about why gear reducers break
When the gear reducer is used for a long time, it will also cause vibration or noise problems, which also indicates that the components of the gear reducer are broken. The following analyzes the causes of gear reducer damage and repair methods:
(1) Gear damage Gear wear mainly includes tooth surface wear, gear breakage or pin hole damage.
(2) The wire hole is damaged at the rolling bearing hole of the gear reducer.
(3) Damage to the surface of the gear reducer shaft, damage to the groove and bending of the shaft.
We can perform self-service and repair and replace parts for common gear reducer failures, as shown below:
For non-tangential damage, such as the groove of the hole, the electroplating process can be used to restore the precision of the original parts. Shaft bending can also be done by pressure straightening. There is no other way to destroy this kind of collapse, only to repair the new parts.
This is just a preventive measure to prevent the occurrence of the incident. To ensure the service life of the gear reducer, the key is to choose the type when purchasing, ensure high safety performance, strictly follow the instruction manual, ensure lubrication, and avoid overloading. If the gear reducer encounters an abnormality during operation, it should be checked as soon as possible and then used after the common fault is cleared.
Micro reduction motor manufacturer: four major operating skills of gear reducer
1. During operation, if the temperature rises above 80℃ or the ambient temperature of the sewage tank exceeds 100℃ and abnormal noise is caused, stop using it, check the cause, make sure to correct the common faults, replace the polishing oil, and then operate it again.
2. When changing the engine oil, you should wait until the gear reducer is cooled down without the risk of burning out, but still keep it moist, because after cooling down, the viscosity of the oil increases and it is difficult to add oil. Note: Disconnect the power supply of the transmission assembly to avoid accidental plugging in.
3. After 200-300 hours of operation, the operation should be stopped and the oil should be changed for the first time. In future use, the quality of the oil should be maintained regularly. The oil that has infiltrated with residue or deteriorated should be replaced immediately. Under normal circumstances, for gear reducers that are in long-term continuous operation, the oil should be replaced every 5000 hours or once a year. Gear reducers that have been out of use for a long time should also be replaced with new oil before re-operation. Gear reducers should be filled with the same oil as the original model and cannot be used interchangeably with oils of different models. Oils of the same model but different viscosities can be mixed and used.
4. Customers should have a scientific and reasonable application maintenance management system, and carefully record the operation of the gear reducer and the problems found during inspection. The above standards should be strictly followed.
Post time: Oct-02-2024